The TOPO2 is a premium off-road camper, built to endure. One thing that sets it apart from other teardrop trailers is our unique approach to body construction. While there are certainly other fiberglass travel trailer options on the market, none are quite like ours. We use a single-piece composite fiberglass body with an infused structural PET core made from recycled milk cartons.
How exactly does fiberglass construction work?
Fiberglass is a durable, reinforced plastic material embedded with woven glass fibers. Before epoxy is applied, fiberglass is a relatively soft and flexible fabric that can take on any shape. Epoxy is essentially the glue that bonds the fiberglass together when it's being molded into its final form. When it came to choosing between the many possible construction methods, we let our design requirements lead the way: to be as light, durable, and sexy as possible. We’re not just trying to make a fiberglass travel trailer, but the best fiberglass travel trailer on the market.
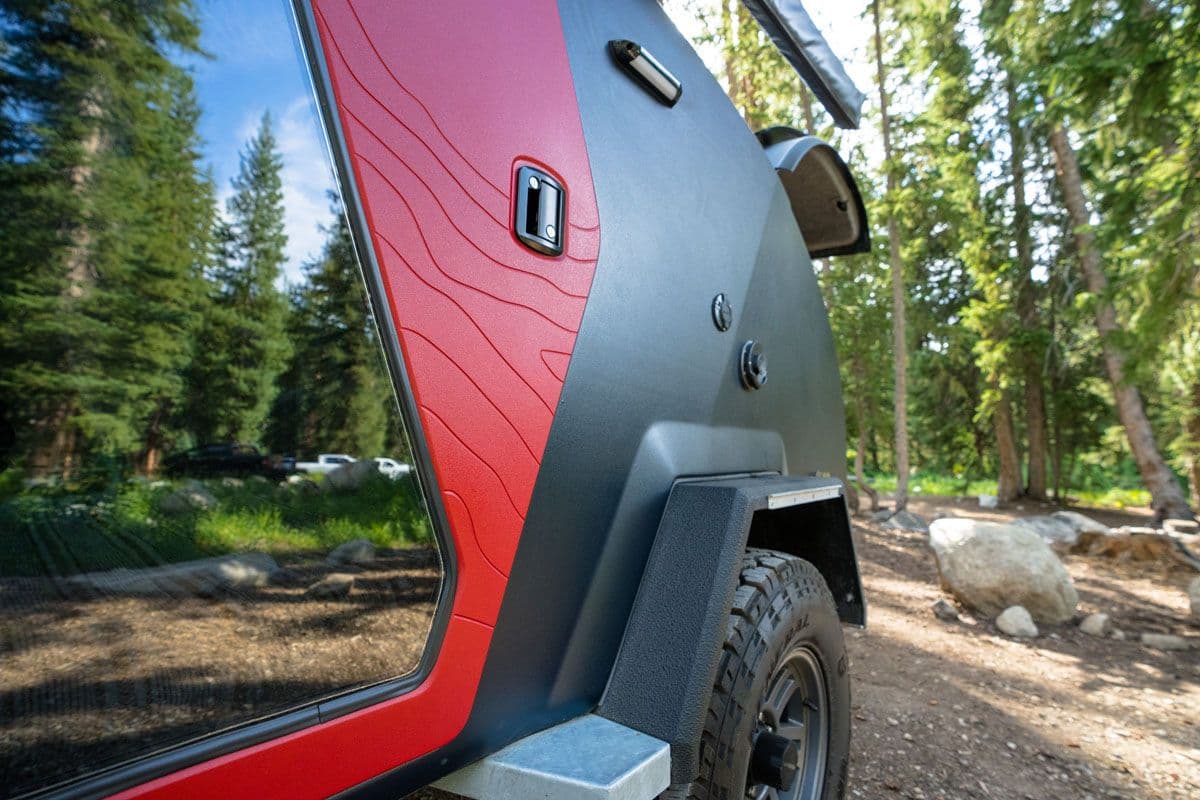
To eliminate as much weight as possible, we had to have a structural composite body. Some fiberglass shells are mostly decorative, with a hidden (and heavy) wood or aluminum frame underneath. For TOPO2, we wanted an infused core to be the primary structural component of the trailer.
To better understand the construction process we ultimately chose, let’s dive deeper into the three main types of molding for fiberglass campers.
Chop & Spray
While chop and spray could meet our standards for lightness and shape, it doesn’t check the durability box. In this process, you use a pneumatic gun to chop fiberglass strands and spray epoxy onto a mold surface. This is primarily used for large-format moldings such as boats, truck bonnets, and larger trailers. Because this method is extremely fast, it is a less expensive option.
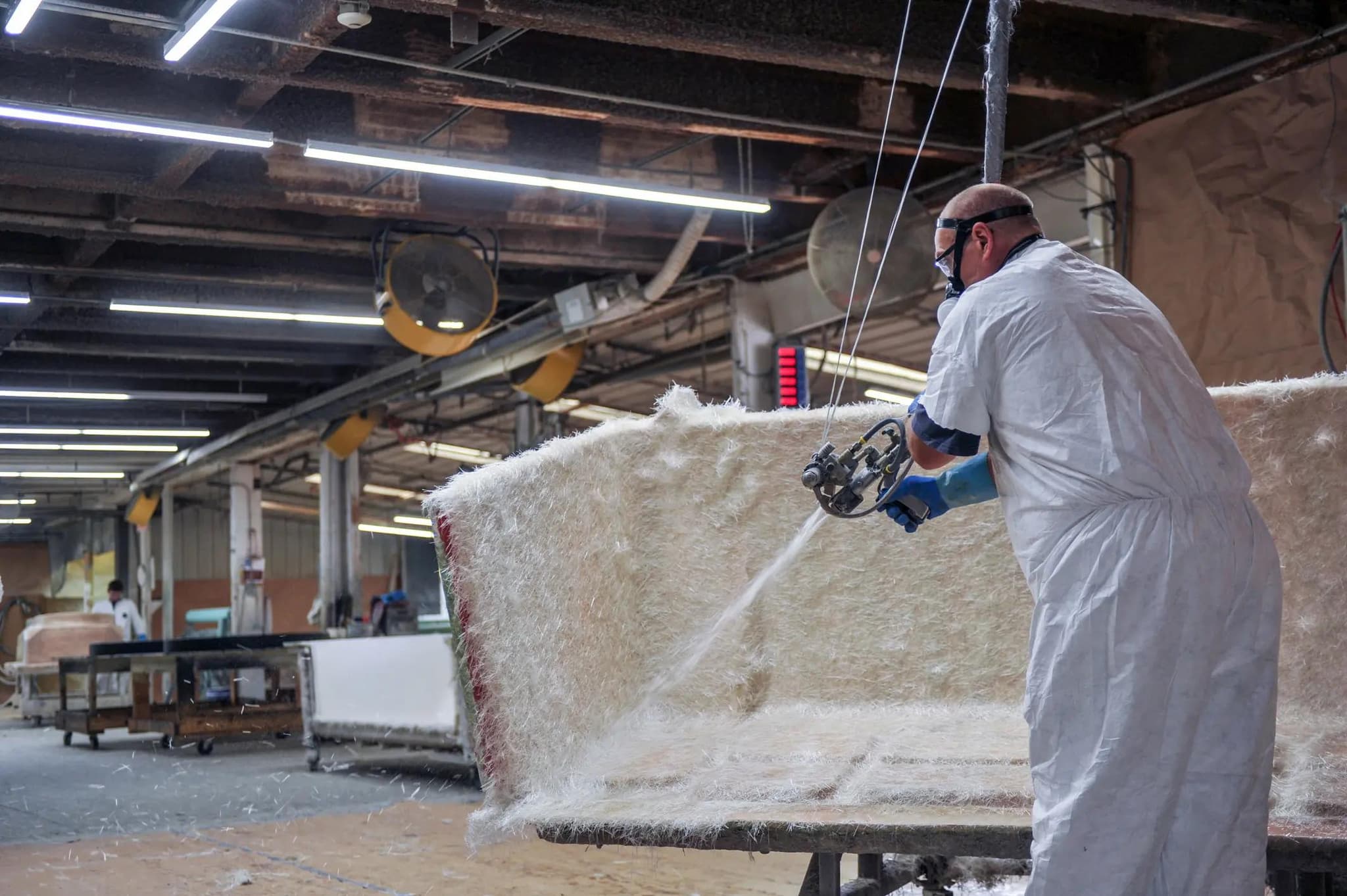
A chopper operator sprays the chopped fiberglass and resin mixture onto the mold surface.
That lower price does come with some downsides though! One of the limitations is that you can’t put any structural component (other than additional fiberglass) into this type of construction, which was a crucial requirement for TOPO2.
Another concern is that, similar to spray paint, it’s very difficult to create a consistent level of thickness. This variability makes it very difficult to achieve a product with reliable weight and durability - two essential requirements of any off-grid camping trailer.
We needed a more precise method to saturate the fiberglass with the epoxy resin, so the degree of unreliability with chop and spray just wasn’t right for the TOPO2.
Hand Lay-Up
The hand lay-up process is a more expensive method because it requires the most manual work, which involves applying fiberglass layers one by one. Then, the craftsmen brush or roll on epoxy, almost like a grown-up paper mache. While some teardrop trailers have opted to go this way, our unique design requires the ability to build structure right into the fiberglass, and that’s just not possible with hand lay-up composites.
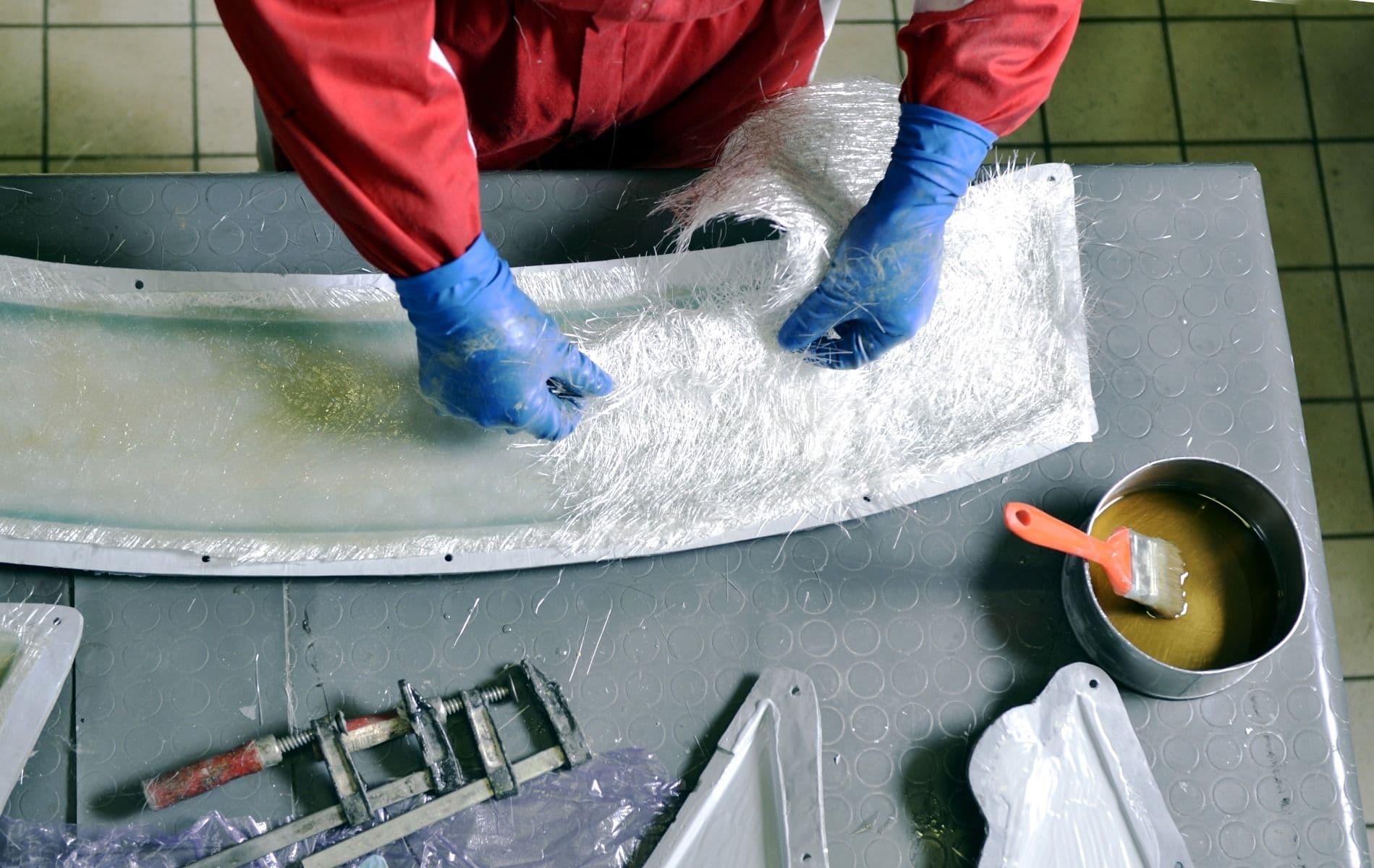
A technician is seen laying fiberglass sheets onto a mold surface. Epoxy resin is then brushed onto the surface to cure it.
We knew this wasn’t the right fit since TOPO2 needs consistent curing. The hand lay-up method simply creates a fiberglass shell with no further structural reinforcement. With this approach, it’s difficult to control the application of epoxy resin. Using a paintbrush or roller leaves too much room for uneven saturation for our taste, and the result can be over or under-saturated. Once again, the durability just wasn’t up to snuff!
Vacuum Infusion
We finally found our Goldilocks porridge using a high-quality vacuum infusion process. Though infusion is costlier because it requires more systems and increased precision, it's definitely the best fit for our product goals.
With infusion, the fiberglass cloth is laid onto the mold using tack adhesive. After that, a large vacuum bag goes over the entire mold to suck the air out and compress everything to be as compact as possible. (Think of those plastic storage bags that flatten puffy comforters with a vacuum!) Then, technicians inject epoxy resin through a port in the bag and use another port to suck the resin to evenly distribute it throughout the fiberglass. This process creates that perfect saturation we wanted - nice and even all over.
An infusion process also allows for other materials to be put into the lay-up. This is how we integrated our unique PET core to build structure right into the fiberglass itself.
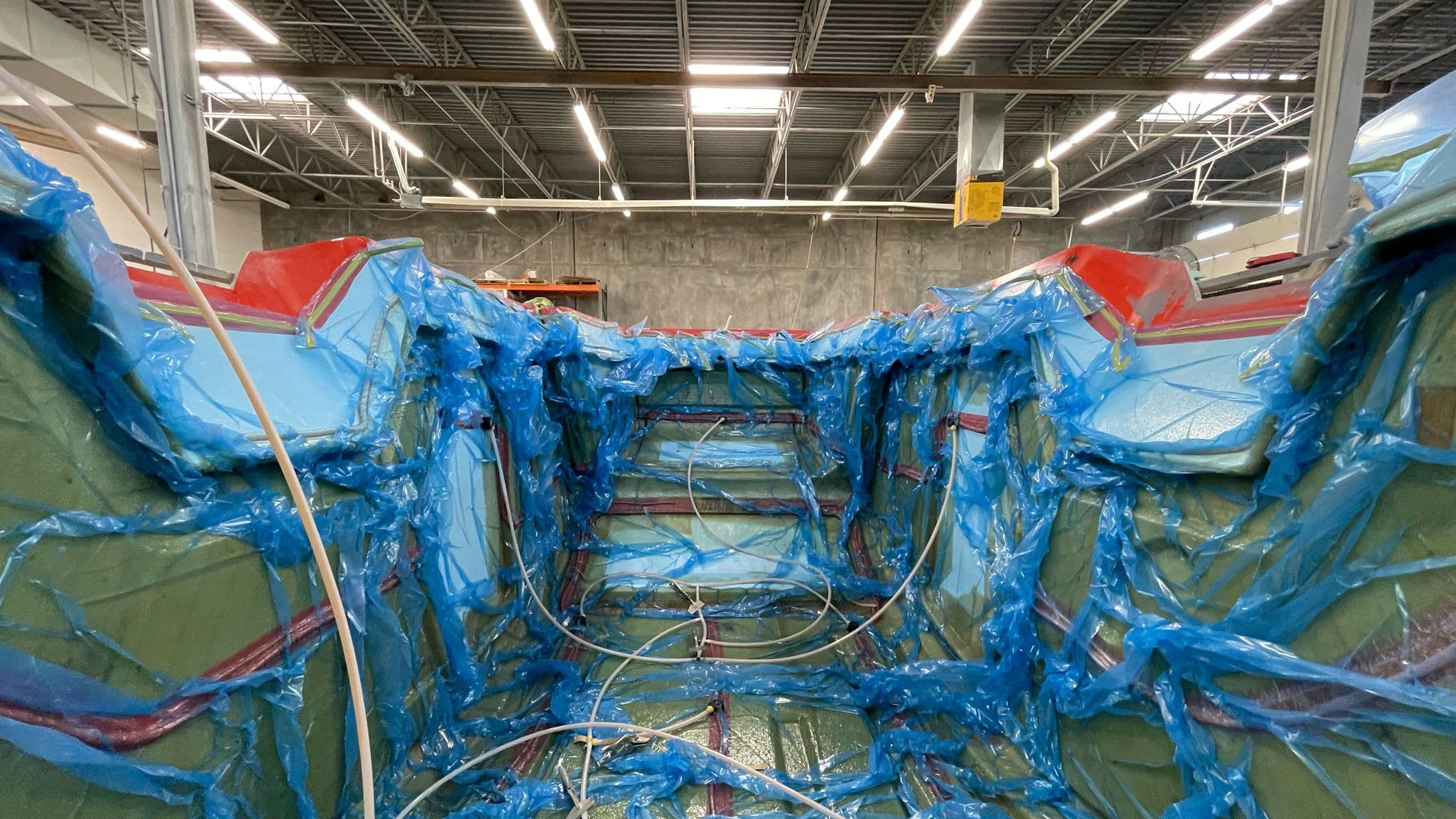
An example of a boat hull using a vacuum infusion process for its fiberglass layup.
Our engineering team carefully considered all of the possible routes when deciding how to best manufacture this revolutionary trailer. With quality, consistency, weight, and strength at the forefront, they explored the available processes through Escapod’s creative lens.
Ultimately, we chose to use an infusion process to construct the TOPO2 body despite the added cost and time. This process allows us to have the structure built right into the fiberglass, giving our camper trailer incredible strength without all the weight - the exact functionality we’re looking for. Not only that, but TOPO2 has a single-piece body and a fully molded gutter system built into the design, making it sleek, seamless, and leak-proof!
We refuse to sacrifice quality on our mission to build the best damn camper known to man. Our composite design is like no other, and we couldn’t be happier with the results.
More About the TOPO2
The TOPO2 is a deluxe off-road camping trailer that provides a truly uncompromised camping experience. Complementing its single floor plan, the TOPO2 comes standard-equipped with a queen-size bed, 21-gallon water tank, water heater, cabin heater, awning, dual side entry doors, a massive vented stargazer window, led lights throughout, YETI cooler on slide-outs, smart charging systems, 140 W solar panel, 120 amp hour lithium battery, 8500 btu stove, 11-lb propane tank and more.
Optional upgrades like an air conditioner, fridge/freezer, iKamper rooftop tent, bike rack, and rock rails, allow you to customize your trailer to match your adventures. With a dry weight of 2000 lbs and a gvwr of 3500 lbs, the TOPO2 is towable by the tow vehicle you already own.
All of this is backed by an industry-leading 5-year warranty. Learn more about the TOPO2 molded fiberglass travel trailer here.
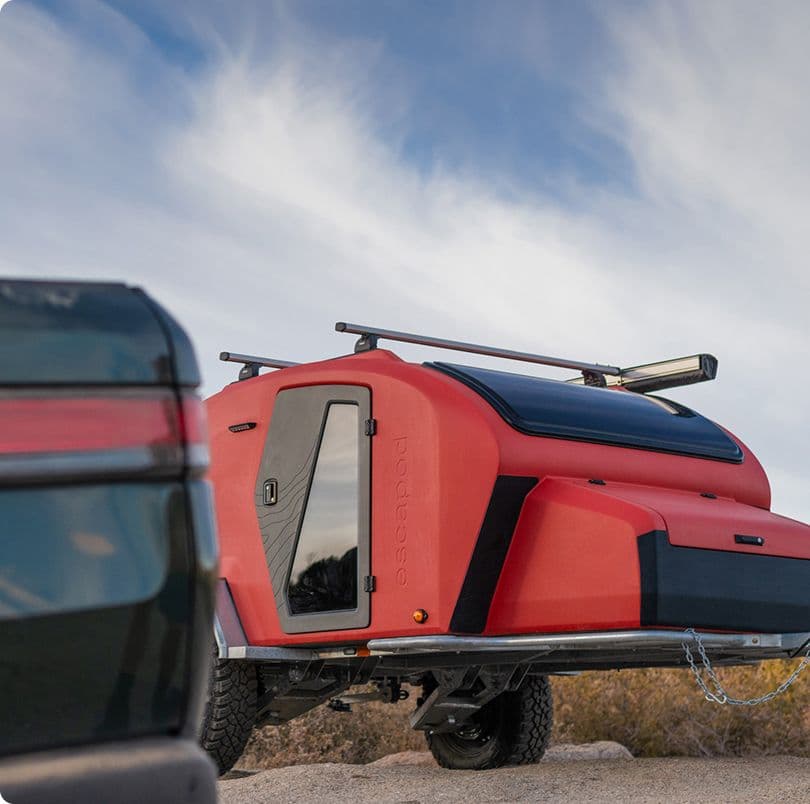